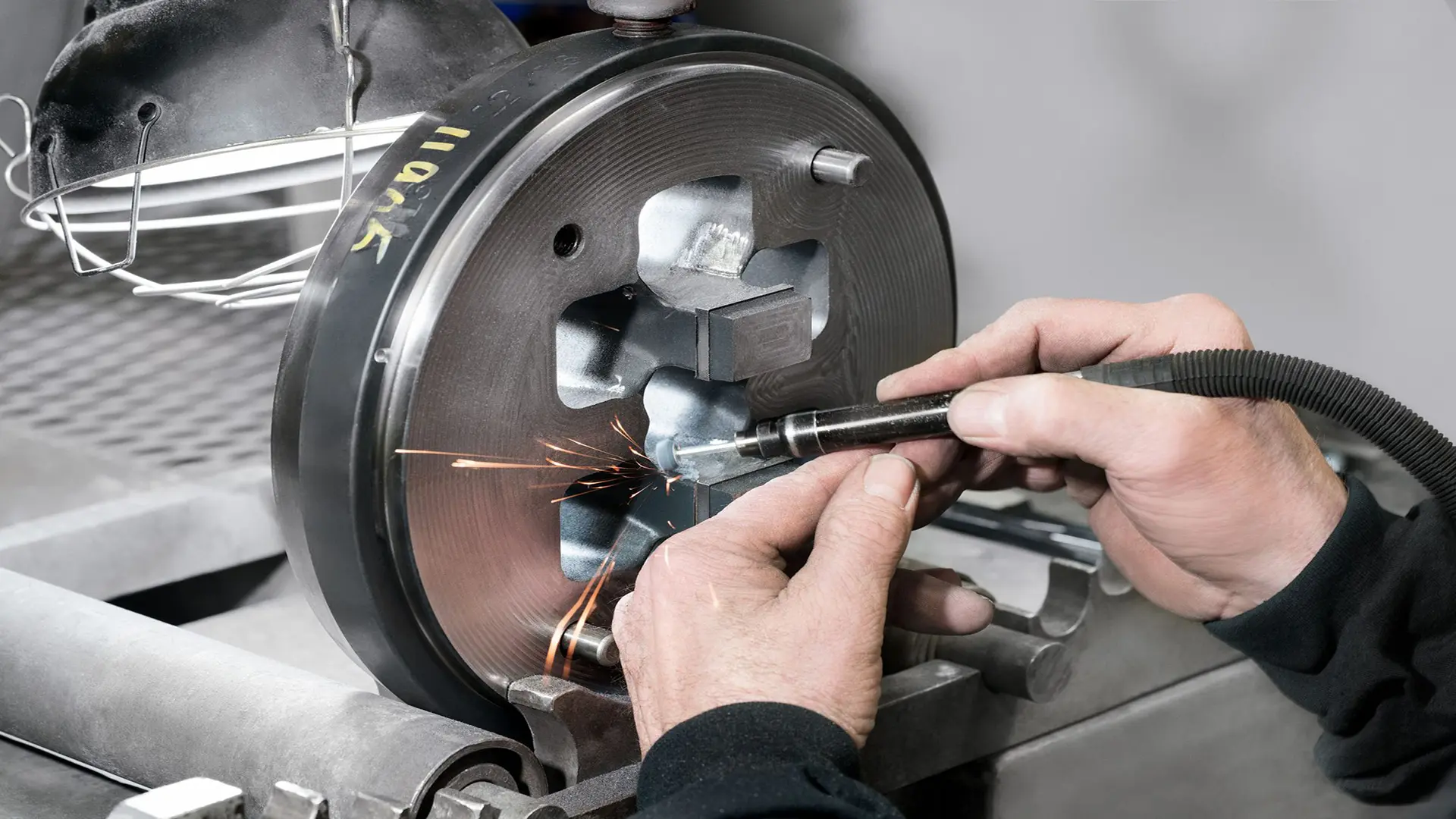
An extrusion die is one type of mold used for producing aluminum sections. These dies are usually made as thick circular plates of hot-work steel and have cavities that create the final shape of the profile.
Due to their high thermal resistance and ability to withstand high pressure, extrusion dies are a suitable option for producing various profiles. With the help of these dies, parts with long lengths or complex shapes can be produced. The extrusion process can be performed cold, hot, or direct.
Extrusion mold design stage
Aluminum mold making is a specialized and technical process consisting of two main stages: mold design and mold manufacturing. These two stages play a crucial role in the final quality of the produced aluminum profile. Mold design is the first and most critical step in producing aluminum extrusion dies. This stage is usually carried out using engineering design software such as CAD, and its goal is to accurately draw the cross-section of the part to be produced. After the 3D design is completed, the mold manufacturing process begins. Mold Manufacturing Stage Mold manufacturing includes two main stages: machining and assembly. In the machining section, the following steps are performed: Initial steel cutting based on the design, initial turning, CNC milling to create the general form of the mold, CNC wire EDM for precise and fine cuts, CNC spark erosion (EDM) to create complex internal shapes, hardening operation to increase mold resistance, grinding and final finishing/polishing to improve surface quality. After machining is completed, the mold enters the assembly stage to be prepared for use in profile production.
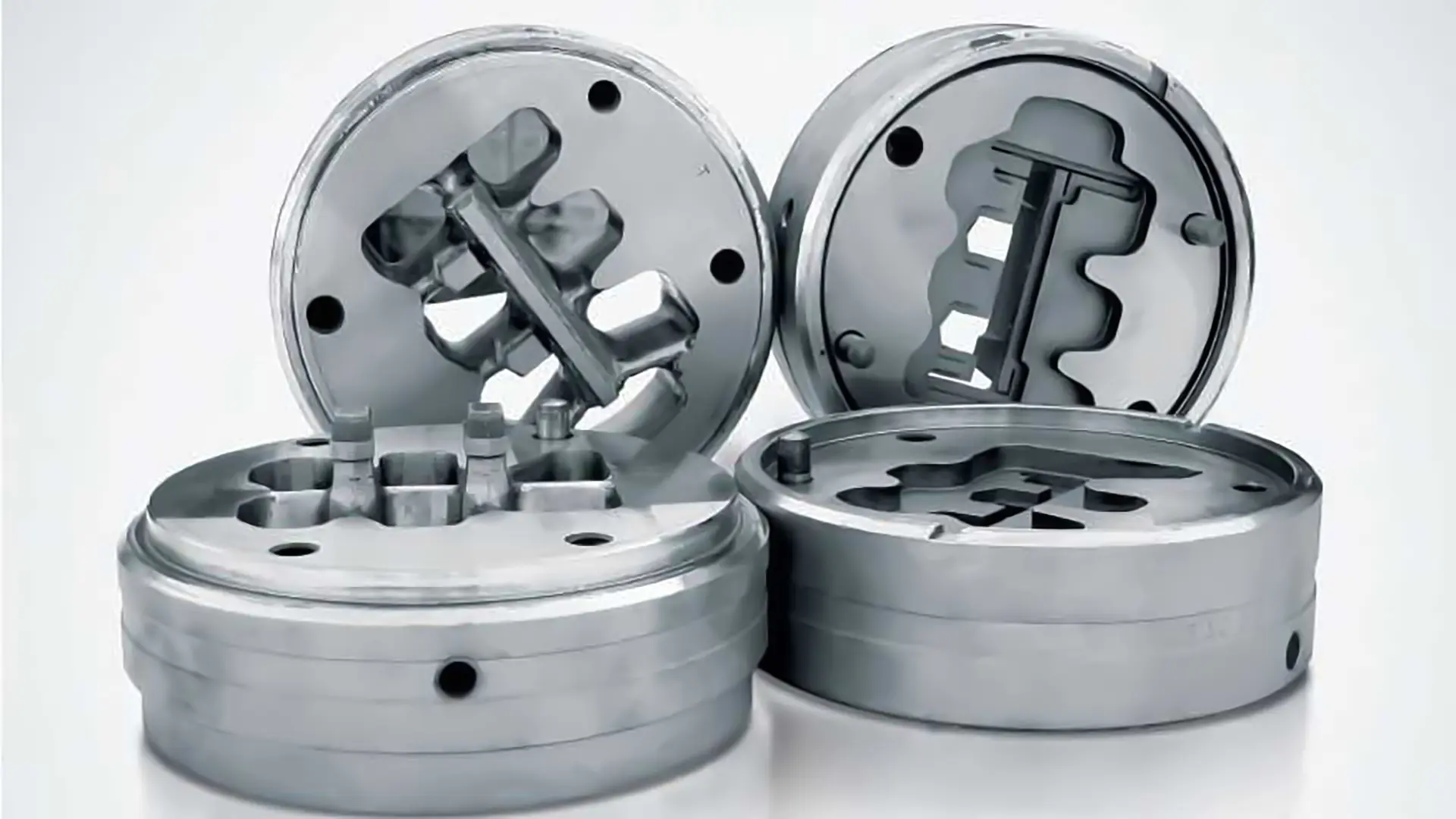
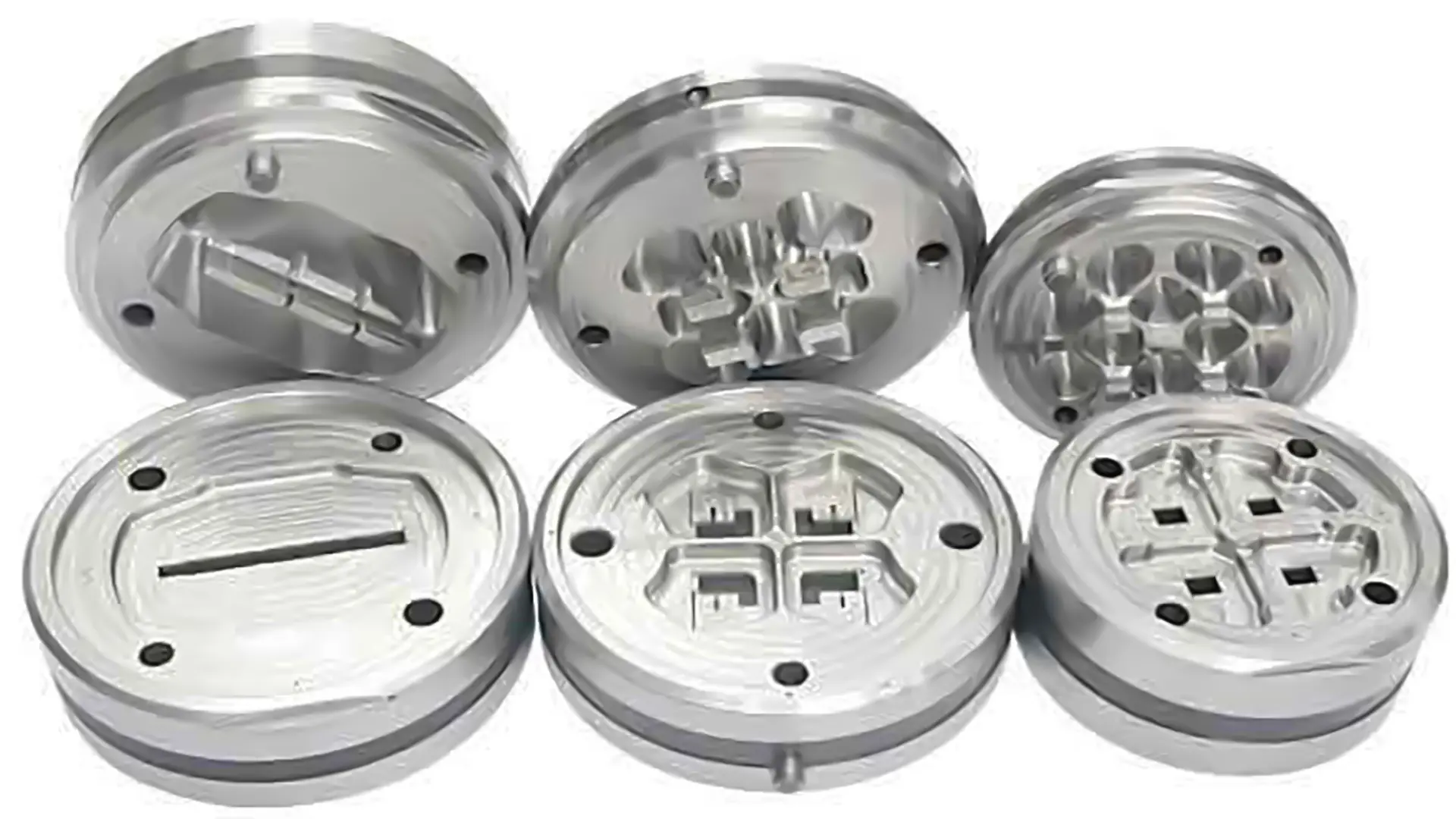
Extrusion process
Extrusion is a continuous or semi-continuous process in which aluminum billets are forced under high pressure through a die to produce the desired profile with a specific cross-section. Factors Affecting Aluminum Profile Extrusion Three main factors play a decisive role in the extrusion process: Temperature Pressure Speed The complex relationship between these factors results in a high tolerance (permissible error range) in this process. Therefore, in the direct extrusion process, frequent monitoring of the process is necessary to ensure final quality. Importance of the Die in Aluminum Profile Quality The extrusion die significantly impacts the quality, precision, and final production cost of the profile. Accurate design and appropriate selection of raw materials for the die play an important role in increasing lifespan, optimizing material consumption, and improving production speed. Advantages of Using Extrusion Dies Ability to produce more complex sections compared to other methods. Capability to shape brittle materials. Increased production speed for high volumes. High precision in creating a uniform cross-section.
Factors affecting the durability and price of an extrusion die
Four main factors determining the quality, lifespan, and price of the die are: The type of steel used (hot-work steel) The geometric and technical design of the die The type of heat treatment and coating (such as nitriding) Proper maintenance and refurbishment methods for the die In Iran, high-quality steels such as Böhler steel from Germany, ORVAR 2M from UDEHOLM, 2344 steel, and domestic examples like Isfahan or Esfarayen alloy steel are commonly used for manufacturing extrusion dies. Important Points in Extrusion Die Design During the design and manufacturing of aluminum extrusion dies, observing the following is essential: Appropriate design considering the press capacity and production conditions. Considering the die's strength against wear and temperature. Reducing manufacturing costs while maintaining production speed and quality. Planning for regular maintenance of the dies to increase their lifespan.
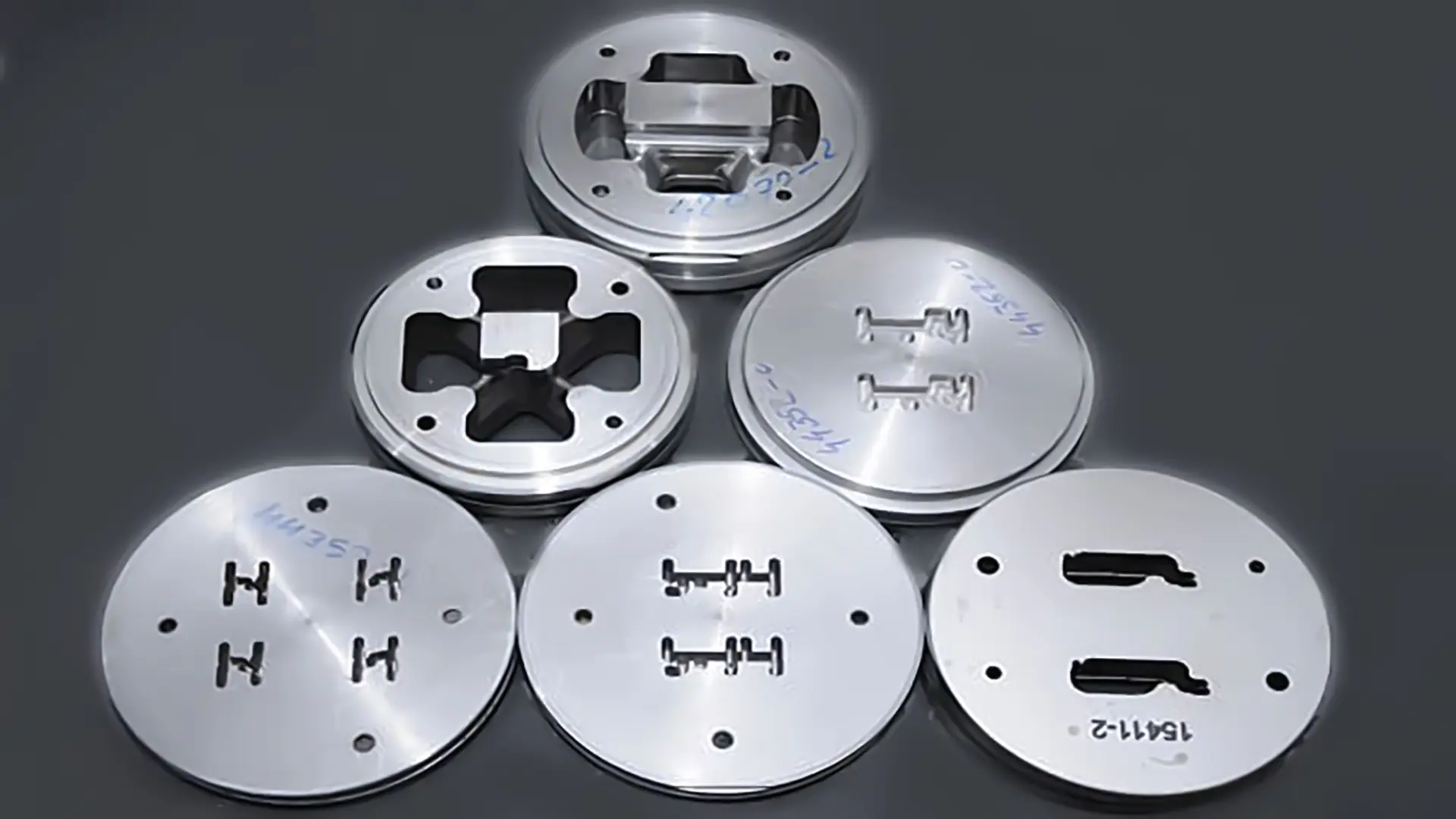