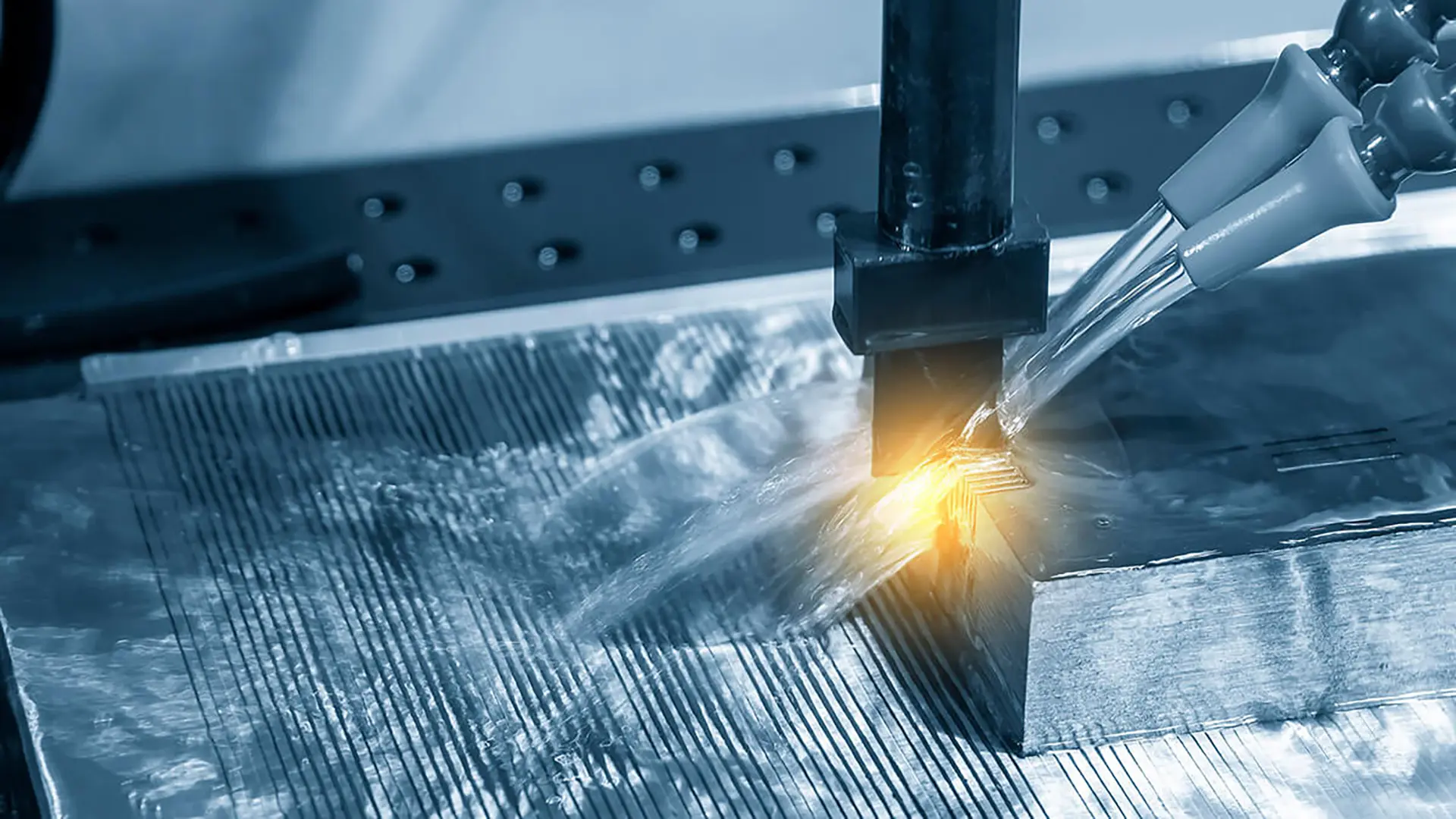
Electrical Discharge Machining (EDM), also known as spark machining, is one of the advanced and precise methods in the mold making and machining industry, utilizing electrical discharges for material removal from metals. This method is particularly suitable for hard and complex parts that cannot be easily shaped using traditional machining methods.
Working principles of the Spark device
In this method, energy is transferred through electrical discharge between two electrodes (typically the tool electrode and the workpiece). This spark discharge results in material removal from the workpiece. The process works as follows: the electrode moves towards the workpiece, and with each generated spark, material is removed from the surface of the workpiece.
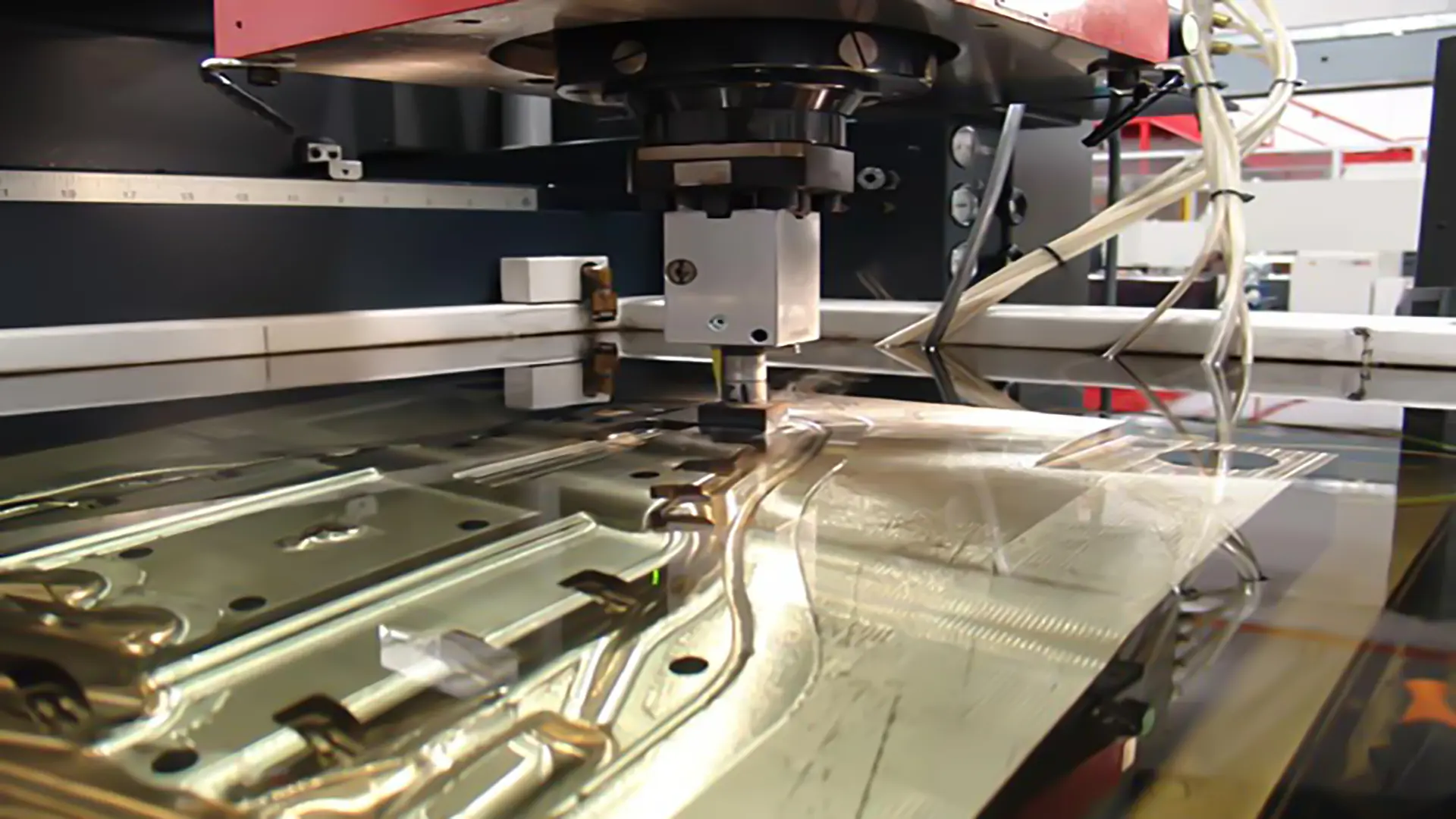
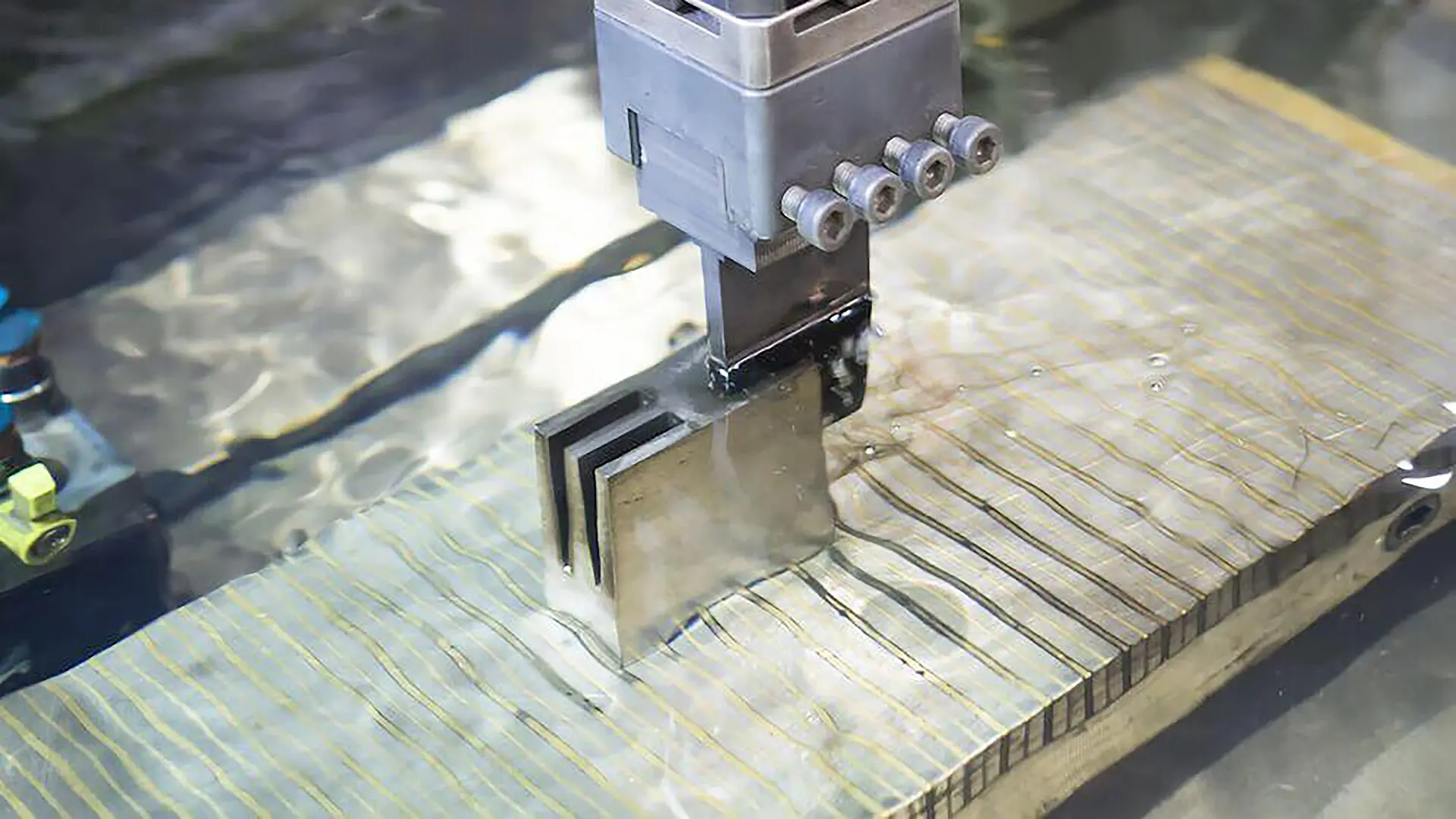
Stages of Spark Machining Operation
Immersion in Dielectric Fluid: The workpiece (usually a mold insert) is immersed in a fluid like oil to prevent excessive heat and to wash away the particles resulting from material removal. Spark Generation: As the electrode approaches the workpiece, sparks with very high temperatures (8000 to 12000 degrees Celsius) are generated, causing material removal. The depth of material removal depends on the spark energy. Reciprocating Tool Movement: The electrode moves vertically; after each spark, it moves up slightly to clear away particles, then moves down again, and this cycle continues until the shape is completed. Electrode Wear and Use of Multiple Tools: The electrode also erodes during operation. For greater precision, multiple electrodes are typically used sequentially: initial ones for roughing and later ones for fine finishing. Circulation and Filtration of Dielectric Fluid: The fluid flows continuously, collects the particles, passes through a filter, and returns to the system after filtration.
Advantages and Limitations
Advantages of Spark Machining (EDM) High Precision: This method is capable of creating the most complex and precise shapes in hard and brittle metals. Ability to Machine Hard Materials: Unlike conventional methods, EDM can be used on metals with high hardness and resistance to machining. Non-Contact Operation: There is no direct contact between the tool and the workpiece in this process, so no mechanical stress is applied to the part. Ability to Machine Complex Shapes: This method can produce various cavities, holes, and complex shapes with high precision. Limitations and Important Points Low Speed: The spark machining process is slower compared to some other methods like milling or turning. High Cost: EDM machines and related operations require expensive equipment, and energy consumption in this method is also high. Need for Multiple Electrodes: For complex and deep operations, frequent replacement of electrodes may be necessary.
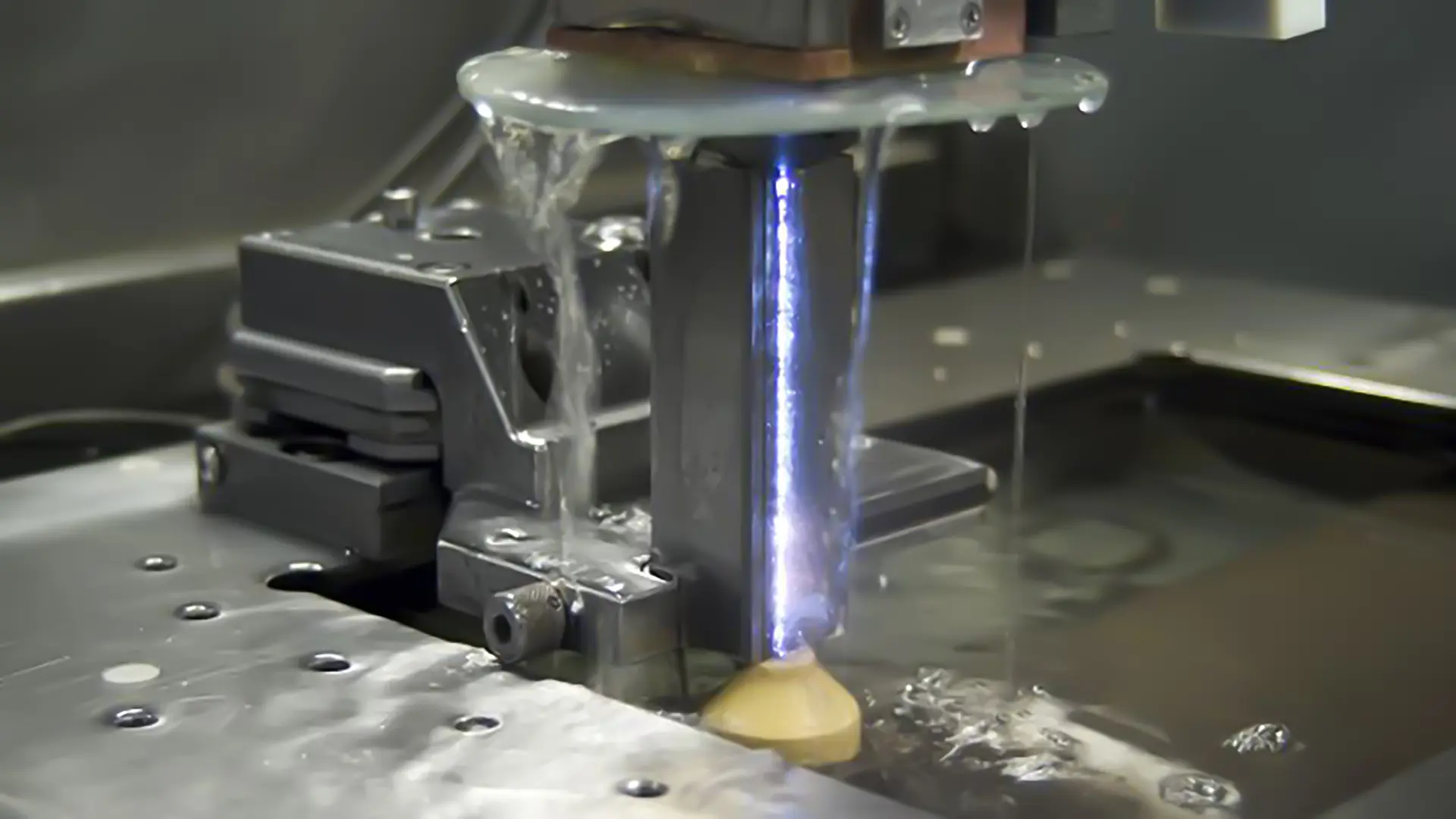
Conclusion
Spark machining (EDM) is an advanced and practical method used in the production of precise, complex, and hard parts. Given its ability to precisely machine hard materials, this method is very useful in the mold making industry and the production of complex parts.