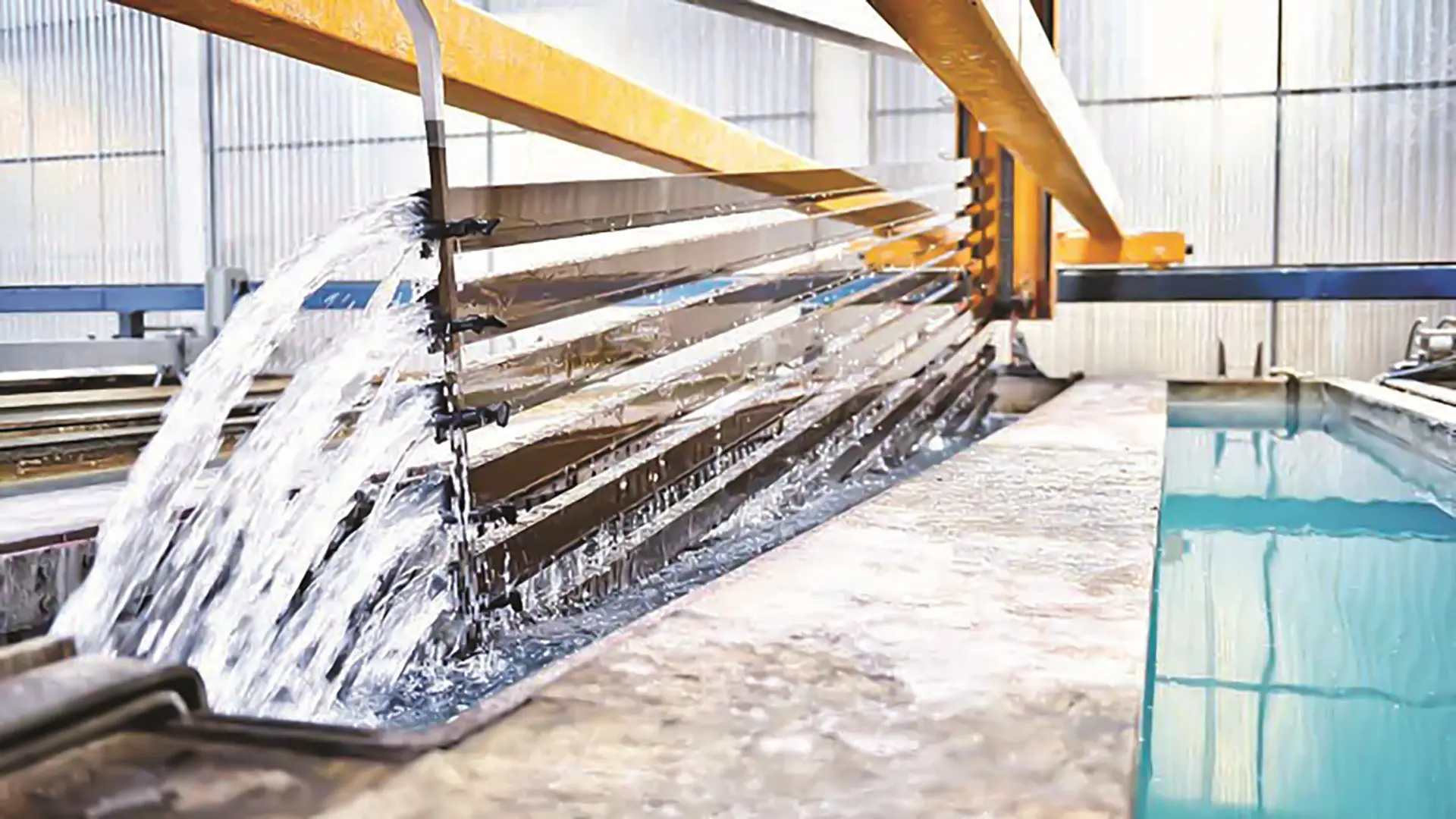
Aluminum is a widely used metal in various industries, including electrical, electronics, telecommunications, aerospace, and automotive, due to its light weight, high strength, corrosion resistance, and environmental friendliness. Its corrosion resistance stems from the formation of an aluminum oxide layer, which, while protective, can dull the metal’s surface. To maintain a bright appearance and enhance resistance further, surface treatments like anodizing are employed.
Because pure aluminum lacks optimal mechanical properties, it’s commonly alloyed with metals like zinc, tin, magnesium, and silicon to improve its strength and formability. These alloys are also suitable for various coating methods, such as electroplating.
Aluminum plating steps
Aluminum plating is a multi-stage process involving cleaning, degreasing, neutralizing, and zincing. These steps are carefully executed to prepare the aluminum surface for subsequent coating with various layers. Cleaning: The first and crucial stage removes any surface particles or contaminants from previous processes. Methods like ultrasonic cleaning are commonly used. Degreasing: This step removes any oily or oxidized layers from the metal's surface. Activated solutions and electrochemical methods (anodic or cathodic) are used for this. Neutralizing: This stage is designed to eliminate any residual alkaline materials from previous steps. Mild, non-corrosive acids are used to prevent surface damage. Zincing: Finally, a protective coating of zinc or tin is applied to the aluminum surface. This thin layer is achieved through zincing or stannating solutions, thereby enhancing corrosion resistance and improving the surface's longevity.
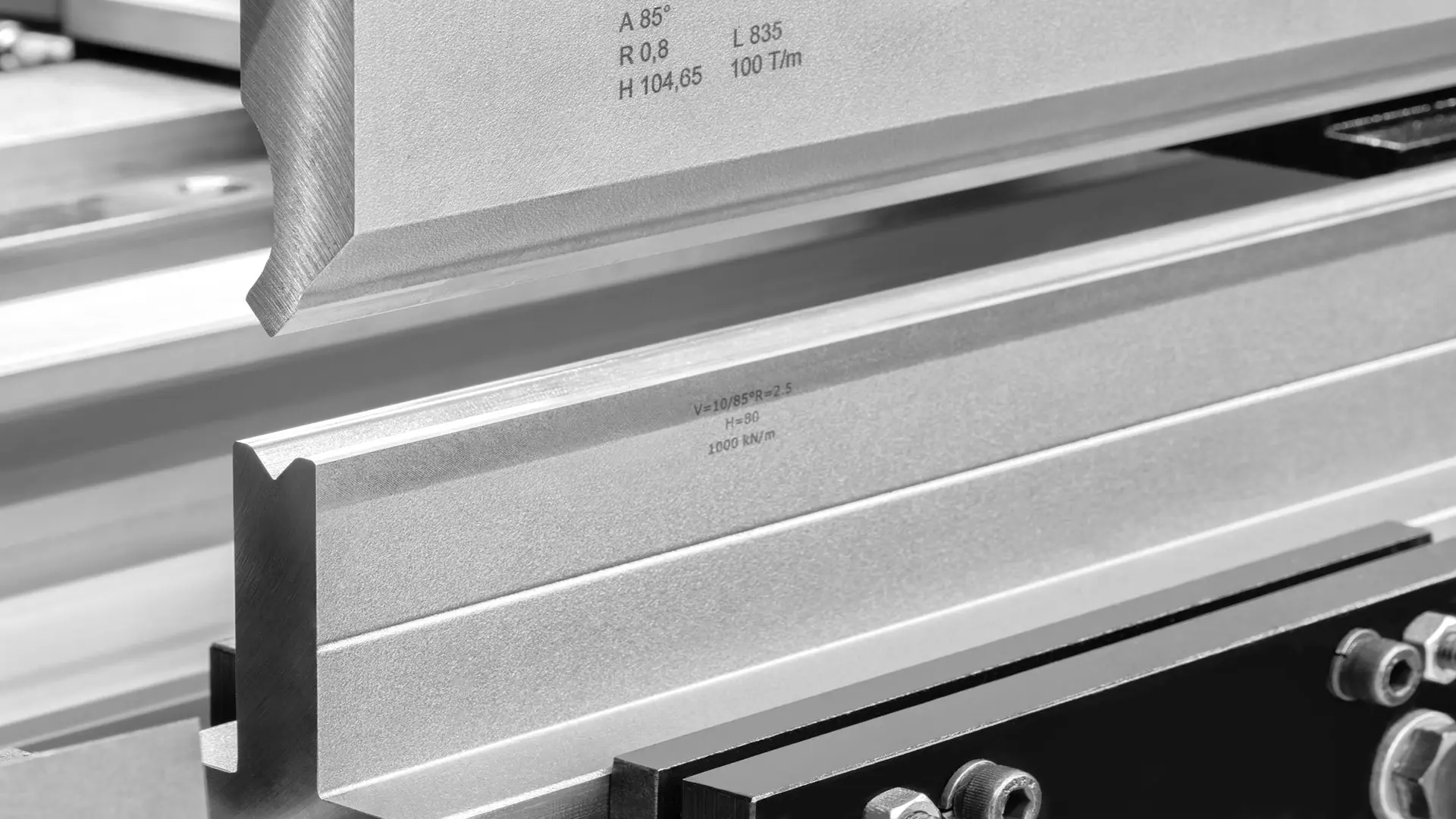
conclusion
Aluminum plating not only enhances the aesthetic appeal of the metal but also significantly increases its resistance to corrosion and environmental damage. This process extends the lifespan of aluminum components and prepares them for use in diverse environments.