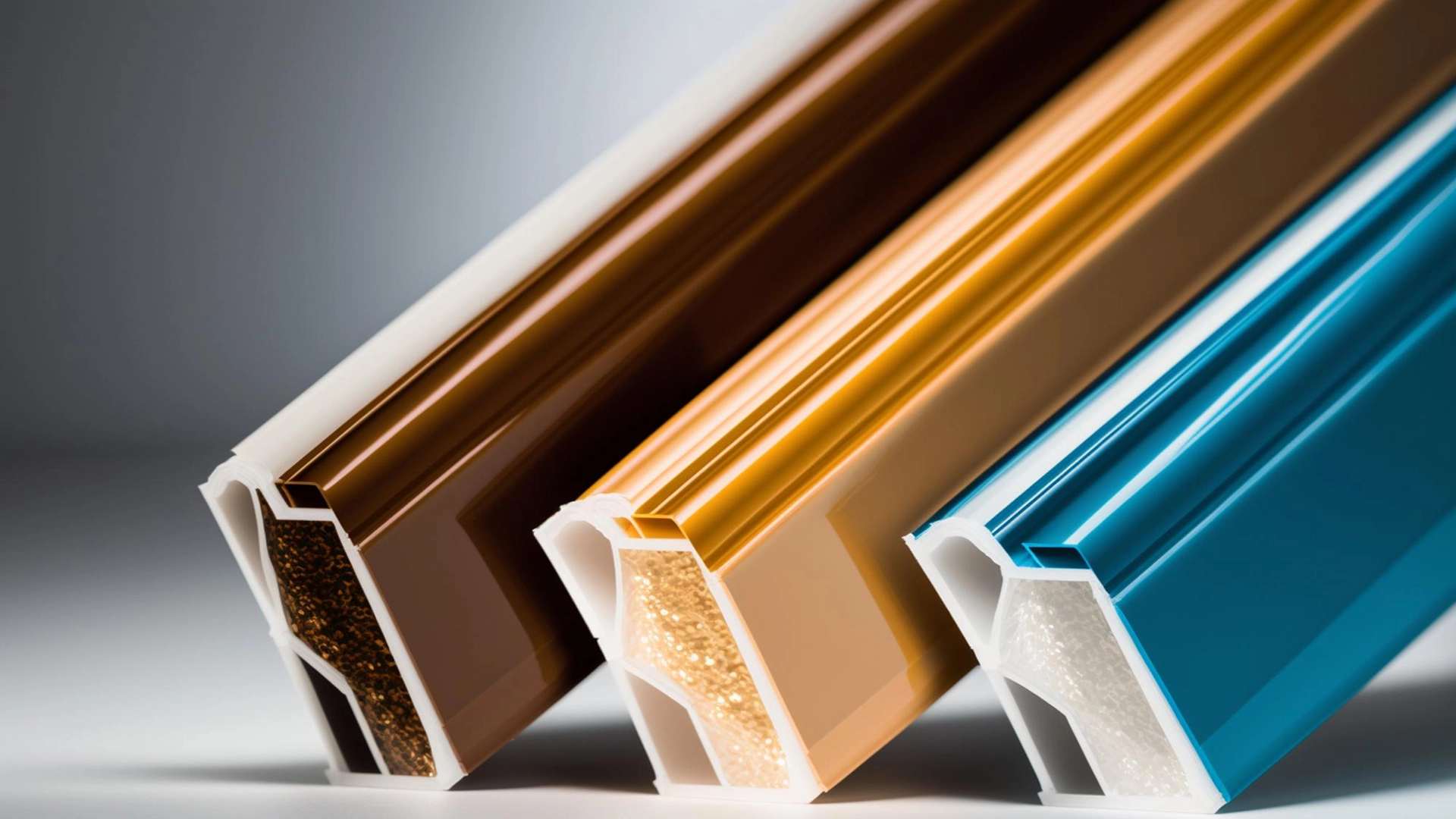
Plastic extrusion is a common and widely used method for shaping plastic profiles. In this process, raw plastic material is melted and forced through a die using a screw. This process is continuous, allowing for the production of long lengths of material. This makes it ideal for creating products like pipes and extrusions. Often, the produced profiles are cut into shorter lengths.
Customs clearance of plastic profiles and molds
Plastic profiles and molds have diverse applications in the production of various parts. These parts include, but are not limited to, strips, angles, channels, hollow sections, door and window profiles, and UPVC (unplasticized polyvinyl chloride) profiles.
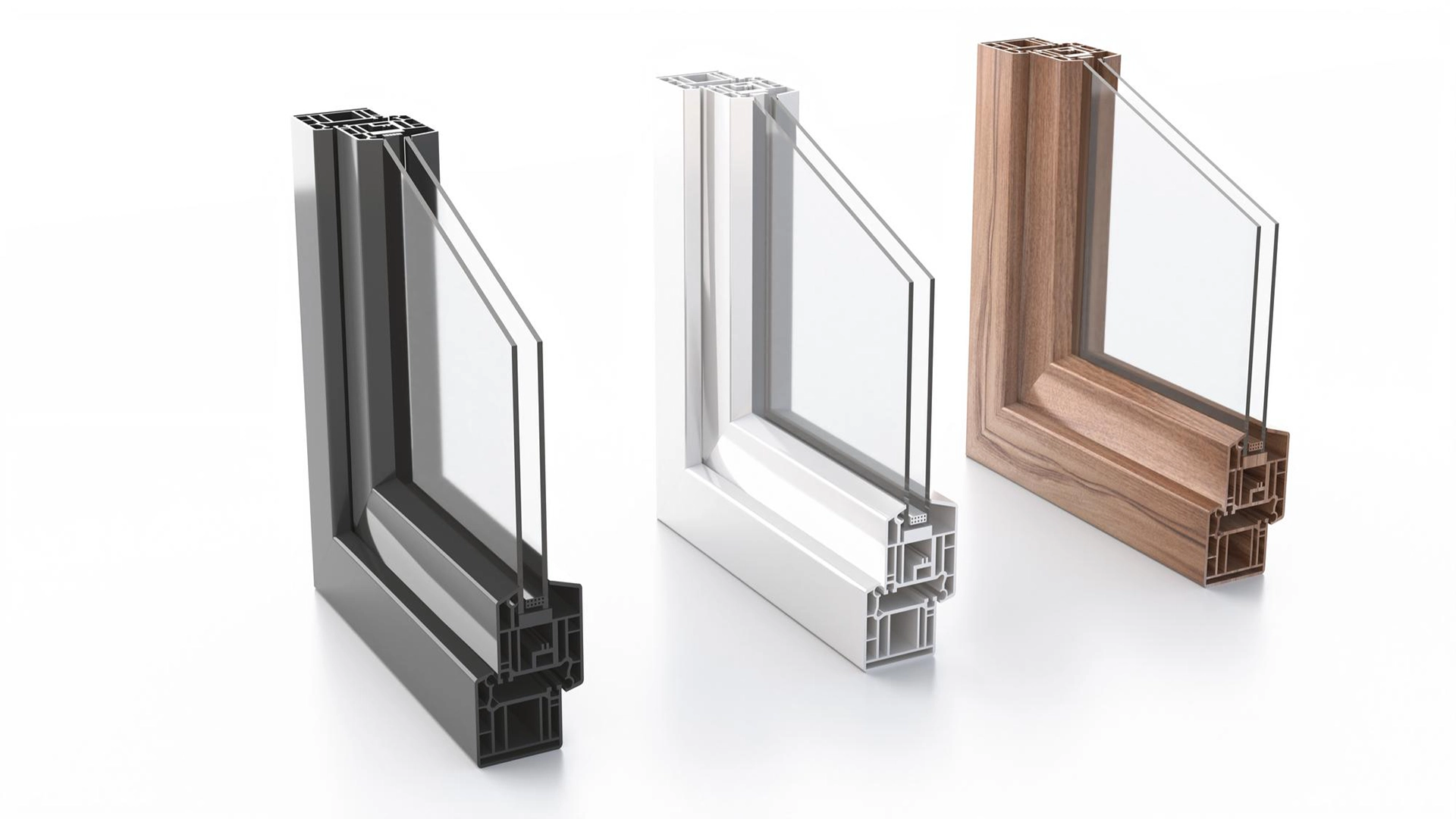
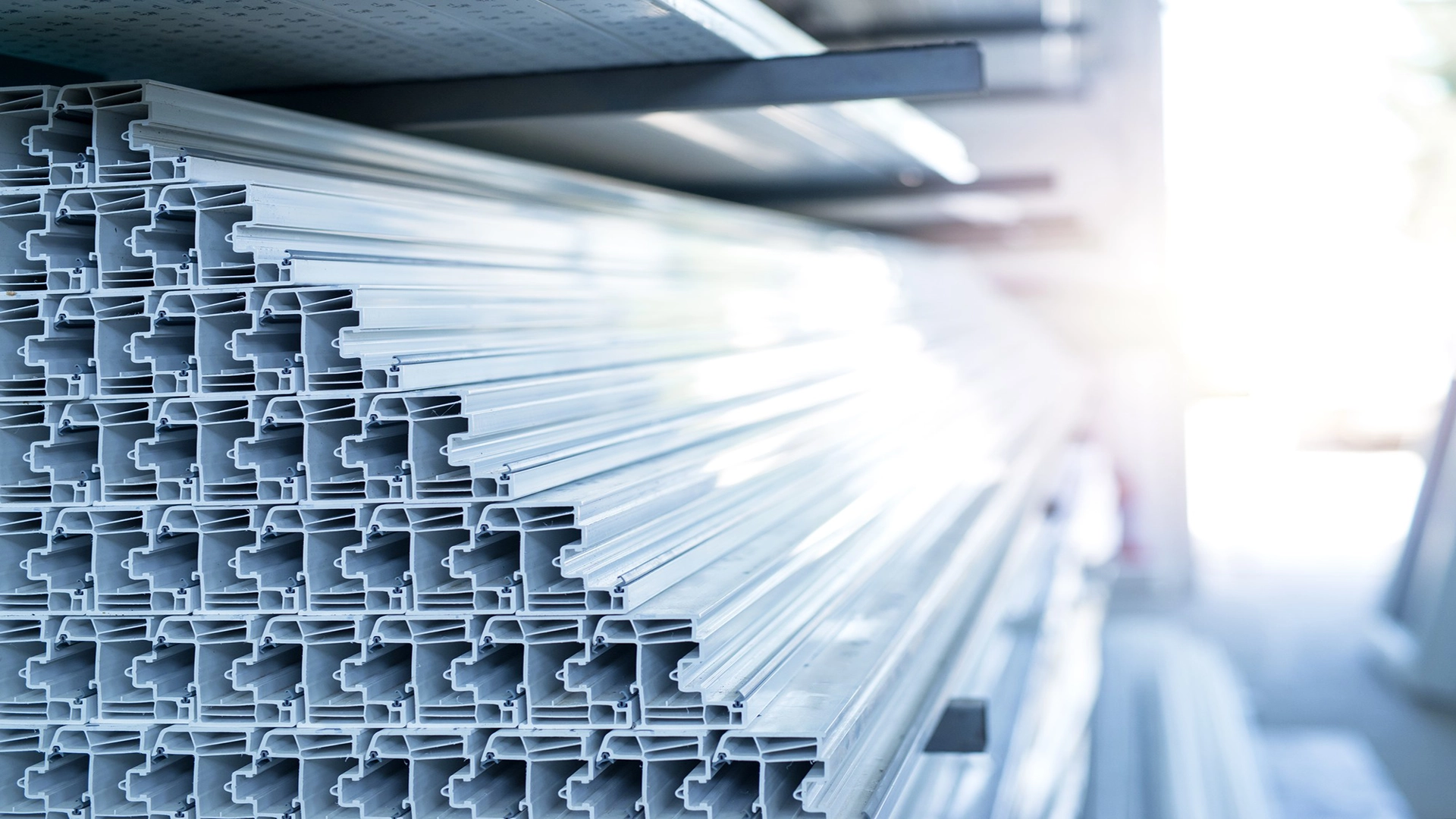
Plastic Profile Production Process
In this process, an electric motor, coupled with a hydraulic drive, continuously rotates the screw within the extrusion machine's barrel. Plastic pellets enter the hopper, and the screw forces them forward. The barrel and screw are heated by external heating elements. This melting and heating process forces the softened plastic under pressure through a die at the end of the barrel. This die has the desired profile's cross-section.
In today’s global marketplace, the use of innovative technology in production and global trade is crucial. Plastic molds are created using injection molding, a process where the final shape of the part is determined by the mold. This mold acts as a template for the desired part, similar in some ways to a gel mold.
Conclusion: Plastic profiles and the extrusion process play a significant role in plastic part production and have found broad applications across various industries. This production method is widely utilized because of its advantages, including the ability to produce parts with consistent length and cross-sections, design flexibility, and lower costs compared to other methods.