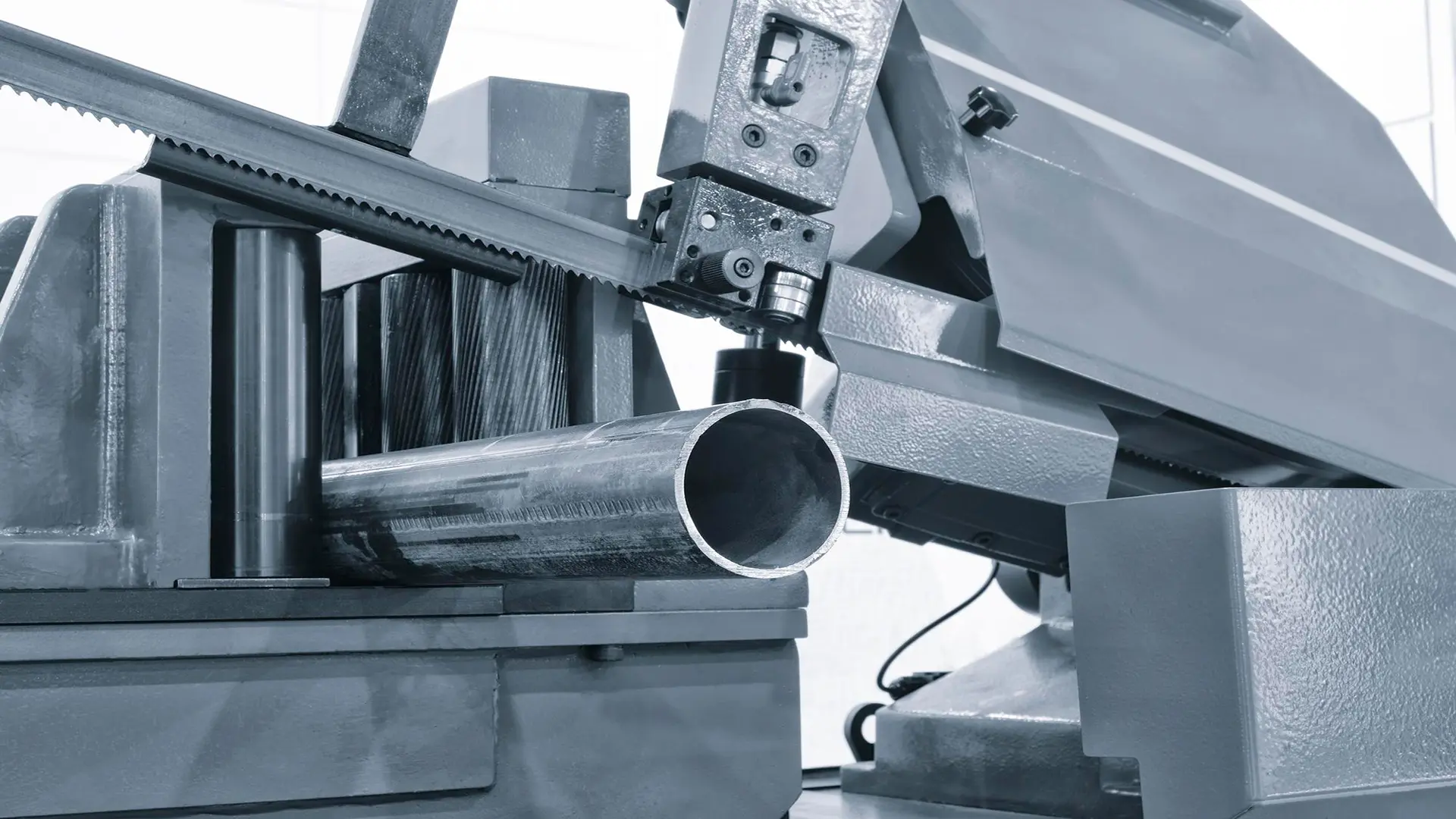
Aluminum is one of the most versatile and widely used metals in metalworking and manufacturing facilities worldwide. While readily machinable, aluminum presents challenges in cutting due to its softness and tendency to heat up quickly. Improper cutting techniques can lead to warping or bending of the material, greatly increasing the time required for the craftsman, and in the worst case scenario, damaging the entire project.
Thus, the proper choice of blade, tool, and technique for precise, flawless cutting is crucial.
Types of devices and methods
Circular Saw (Bandsaw): Common tools for straight cuts in aluminum sheet metal. Using specialized aluminum-compatible blades increases accuracy and quality, though not ideal for thick sections. Best for quick cuts and smaller areas. Power Saw: Suitable for cutting smaller aluminum pieces like tubes and bars. Interchangeable blades allow for replacement when worn or damaged, making it good for finer cuts. CNC Machine: An excellent choice for precise and engineered cuts. These machines efficiently cut thick aluminum sheets or bars into final components. High precision and repeatability are key features. Plasma Cutting: Utilizes a jet of ionized gas exceeding 20,000°C to melt and remove material. The electric arc is focused through a nozzle to create extremely narrow, precise, and fast cuts. This method works well for cutting electrically conductive alloys like steel, aluminum, nickel, and titanium. Drilling: Using drills and CNC machinery, this method performs cutting operations, creating holes, slots, or geometric shapes in the material. Suitable for creating specific patterns or designs on aluminum pieces.
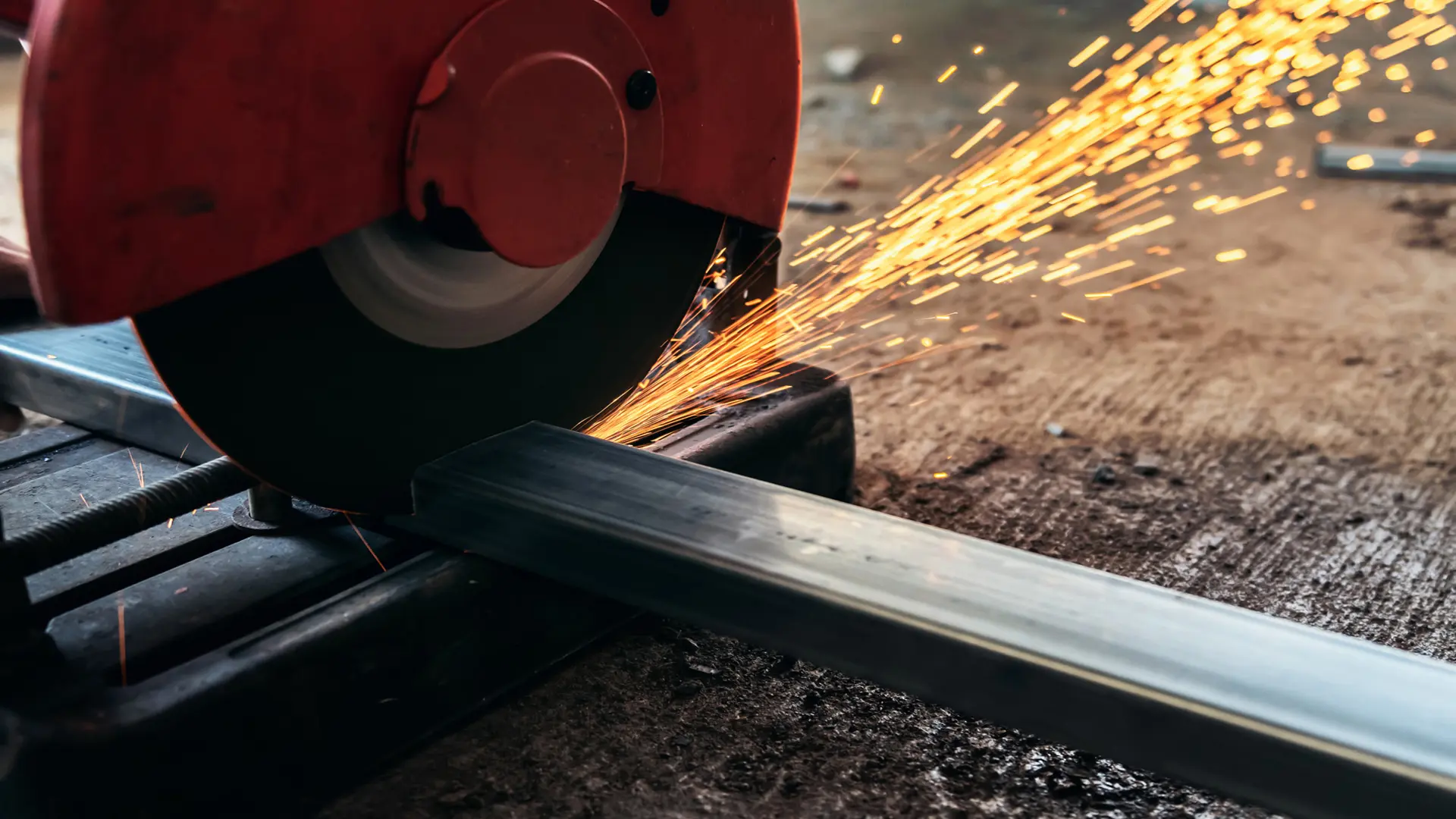
Conclusion
To cut aluminum accurately and efficiently, it is important to know the right tools, follow the correct sequence of steps, and use quality materials. Following these steps will not only increase the final quality, but also save time and money.